British based G3 Systems wins €100M contract to supply Containers and Flatracks for the Netherlands Ministry of Defence
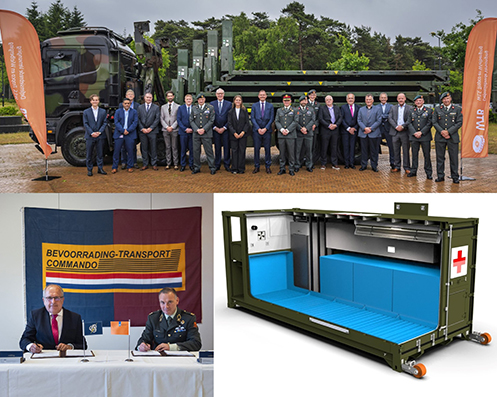
G3 Systems Limited, a British company with approaching 25 years of operationally proven expertise in the design and production of deployable infrastructure solutions, has won a major new contract to supply the Netherlands Ministry of Defence with circa 700 flatracks and containers, as part of their Wissellaadsystemen, Trekker-opleggercombinaties and WielBergingsvoertuigen (WTB) programme. The contract is worth €100M and consists of a 30-month delivery phase followed by a 15-year support phase.
The Netherlands WTB programme has 3 distinct elements – Trucks, Trailers & Semi-Trailers and Physical Distribution Systems. The contract for the flatracks and containers is the largest of 3 separate parts to the Physical Distribution Systems. The G3 Systems contract is for the provision of over 400 general purpose flatrack units and associated equipment, and 270 specialist containers for the storage and transportation of general stores, medicinal items, ammunition, POL & chemicals. The container sub-systems include power generation, HVAC CBRN filtration, medical refrigeration and equipment tracking & monitoring. There is also a contract option to increase the units delivered under the initial contract by up to 100%. Both the flatracks and containers are to be capable of worldwide deployment by all means of transport.
The project demonstrates true collaboration with G3 Systems’ established global supply chain, with a large part of the integration to be completed by European manufacturing partners in conjunction with G3 Systems programme management, project expertise, design and support services.
Nick Rose, Managing Director of G3 Systems said, “This is a momentous landmark in the history of G3 Systems, and I am incredibly proud that the hard work, dedication, professionalism and expertise we hold at G3 Systems has been recognised with this contract award, won in open competition. Clearly there is a tremendous amount of work to do, and we have already bolstered our team in order to be ready to deliver in the 30-months delivery timeframe, whilst making sure we sustain and grow the remainder of our business.” He added: “This has been a true team effort, which is a game changer for this organisation and one that will elevate our provision of deployable infrastructure to the next level. Thank you to everyone who has helped to make this happen.”
Image caption: G3 Systems sign contract with Netherlands Ministry of Defence
G3 Systems completes Stage 1 on their third overseas infrastructure contract with the UK’s Foreign and Commonwealth Development Office (FCDO)
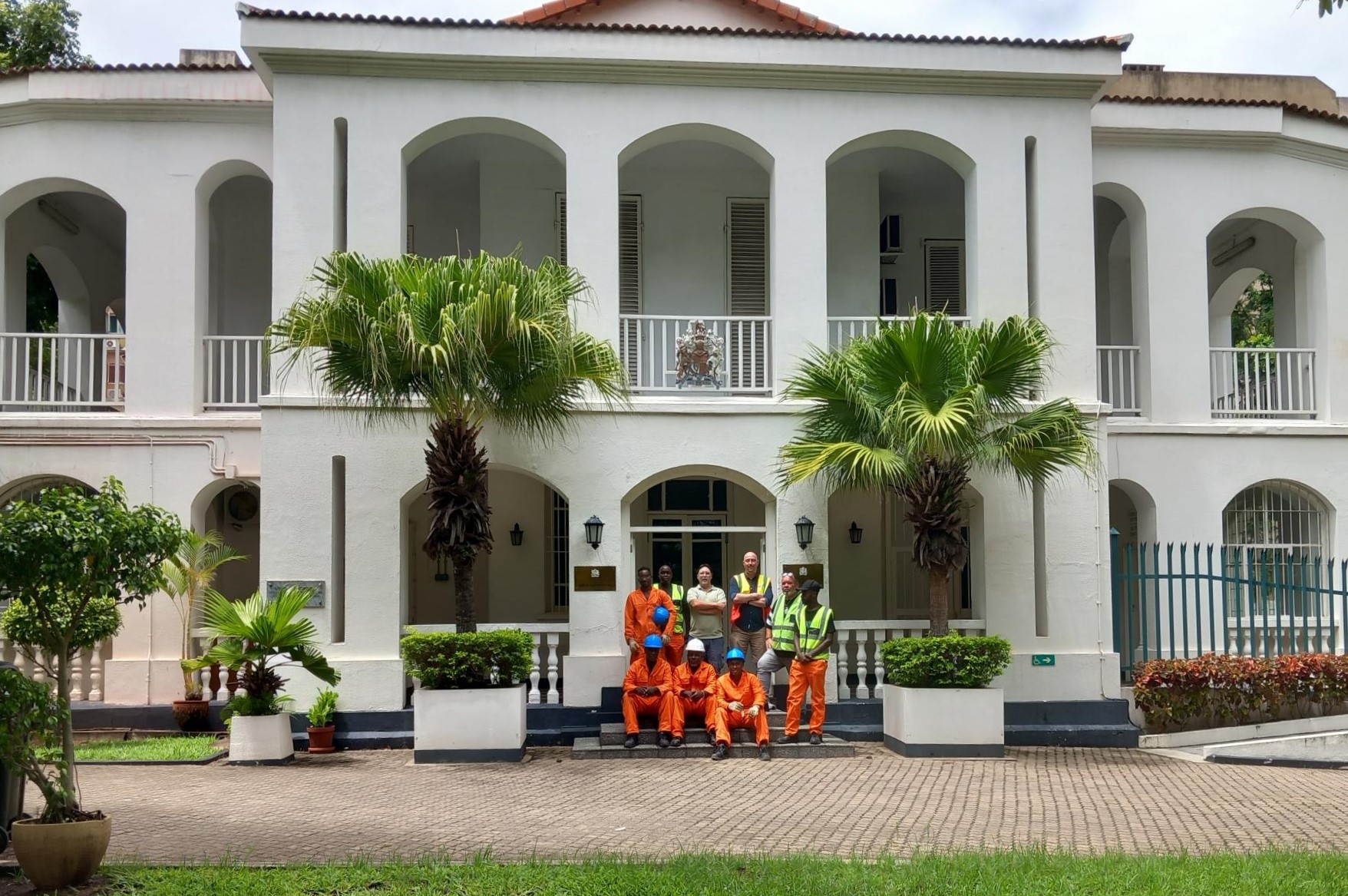
G3 Systems Limited, the British company with nearly 25 years of operationally proven expertise in designing and producing deployable containerised solutions and providing infrastructure support to military and government organisations in remote locations across the globe, has just completed the Stage 1 surveys of their third overseas construction project for the FCDO. In the last 12 months, G3 Systems has announced contracts to refurbish two other FCDO locations in Lagos and Luanda. This latest contract is for the refurbishment of the British High Commission in Maputo, Mozambique.
The contract was awarded following a competitive tendering exercise run by the FCDO and is a combination of initial structural and civil surveys (Stage 1) followed by the main refurbishment works (Stage 2). It includes the construction of a single-storey extension, remodelling of the existing building, improvements to internal facilities and external landscaping. The Stage 2 works will take approximately 18 months to ensure fully compliance with current regulations and are designed to meet the highest standards of quality, health and safety, sustainability and security.
Nick Rose, Managing Director of G3 Systems said, “We now have extensive experience of delivering on complex overseas construction projects in remote locations for the FCDO. This is just another example of our expertise in action. G3 Systems has worked with the military on high quality complex construction projects in remote and challenging locations for many years and it is fantastic to see these skills supporting UK national interests elsewhere in the world. I am also really looking forward to sharing more good news soon in other areas of our business.”
Image caption: British High Commission Maputo, Mozambique
G3 Systems awarded contract by UK MOD to deliver additional deployable Mobile Roller Brake Test systems
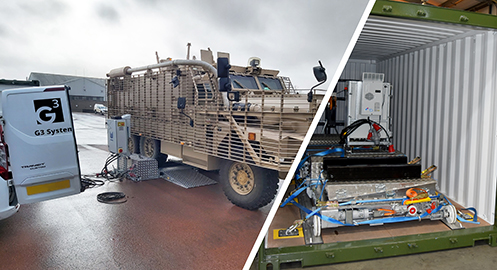
G3 Systems Limited, the British company with over 23 years of operationally proven expertise in designing and producing deployable containerised solutions has been awarded a contract to deliver six more Mobile Roller Brake Testing (MRBT) systems for Defence Equipment and Support (DE&S). The contract has been placed by the MoD’s Operational Infrastructure team under Project Amphora.
G3 Systems were first contracted to deliver 12 MRBT’s in 2018 and have been subsequently tasked by DE&S, in June 2024, to provide 6 more new MRBT containerised solutions that are fully compliant with current regulations, compatible with current generic operational base architecture, such as Field Electrical Power Supply (FEPS), and critically SIM 14 compliant. Delivery will be complete by March 2025.
Project Amphora is a significant initiative aimed at providing comprehensive support for multiple containerised deployable systems that are critical to sustaining military operations. This project is a cornerstone in the MoD’s operational infrastructure policy to ensure that various deployable systems remain at high operational standards, swiftly and efficiently. This recent contract for G3 Systems is a perfect example of the UK MoD leveraging industry’s expertise to ensure that military mission critical vehicles remain operationally safe and ready when deployed overseas or on exercise.
In addition to the normal range of demanding military operational specifications, and the requirement to test vehicles up to 20 tonnes per axle with a maximum wheel diameter of 2 metres, the MRBT systems also have to meet the stringent testing requirements of SIM 14. This means adherence to a specific set of guidelines and standards established by the UK Health and Safety Executive (HSE) for the inspection and maintenance of braking systems in heavy vehicles, particularly those used in industrial and commercial settings. These regulations remain applicable for military vehicles even when deployed on operations. Inherent in the G3 Systems design is consideration for the end user. Using their vast experience and expertise in providing such systems for Defence, G3 Systems ensured the MRBT can be fully operational using two trained operators in under two hours from deployment and be ready to move in less than an hour.
Nick Rose, Managing Director of G3 Systems said, “We are delighted to be supporting the UK MoD again with the MRBT capability under Project Amphora. This is an excellent way for DE&S to use existing partnerships with specialised SMEs to leverage our expertise in providing agile and effective solutions, ensuring that the military can rely on robust infrastructure even in the most demanding environments.”
Image caption: MRBT in action
G3 Systems wins overseas construction works contract for security improvements for British Embassy in Luanda, Angola
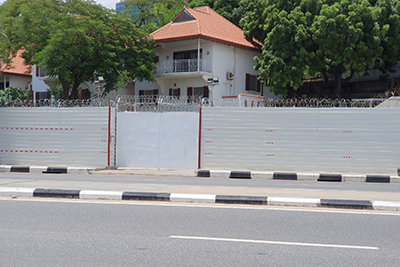
G3 Systems Limited, the British company with over 20 years of operationally proven expertise in designing and producing deployable containerised solutions and providing infrastructure support to military and government organisations in remote locations across the globe, has just started construction works to improve the facilities and security of the British Embassy in Luanda, Angola.
The contract, awarded following a competitive tendering exercise, is a mix of demolition, refurbishment, new build and security improvement works estimated to take 15 months. The project involves a number of complex elements that will have a significant benefit to the location including drainage remedial works, installation of a sewage treatment facility, updating and installing new M&E systems and extensive repairs, improvements and construction of security features for the compound. In addition to the specified construction works, G3 Systems will also be seeking to complete a number of local sustainability/charity projects to support the local community.
Nick Rose, Managing Director of G3 Systems said, “This is another superb example of how G3 Systems are able to deliver high quality complex construction projects in remote and challenging locations. We have years of experience in supporting military operations overseas and I am very pleased that we are now able to use that hard earnt expertise to support UK national interests elsewhere in the world. It is also very rewarding for the team to be helping the local community and improving sustainability by effectively recycling and repurposing valuable materials.”
Image caption: British Embassy in Luanda, Angola
G3 Systems breathes new life into the British Army’s Tactical Containerised Dog Accommodation
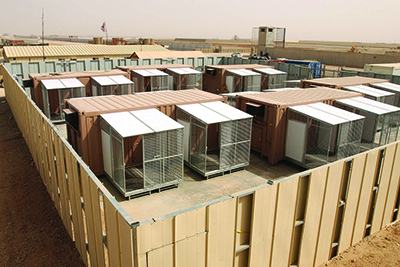
G3 Systems has announced a rolling refurbishment programme, contracted by the UK MoD’s Defence Equipment and Support (DE&S) agency, to extend the working life of their operationally proven and highly acclaimed Tactical Containerised Dog Accommodation (TCDA) for use by 1st Military Working Dogs (MWD) Regiment, based at St Georges Barracks, North Luffenham, Rutland.
The G3 Systems designed and manufactured TCDA capability was first delivered into service in 2008 as an Urgent Operational Requirement (UOR) to accommodate search dogs operating in the extreme conditions of Iraq and Afghanistan. As the Military Working Dog capability expanded, and with an ever-increasing IED threat in theatre, a further 12 TCDA systems were rapidly procured and delivered into service in 2011. All the TCDA systems were initially permanently deployed in Afghanistan until they were returned to the UK in 2014 for use on future operations. On their return, the TCDA were refurbished by G3 Systems prior to their relocation for use at North Luffenham, by 1st MWD Regiment. Since then, the TCDA capability has remained in full operational use in the home base, deployed on various operations and are now maintained at readiness to deploy at short notice as required.
This year G3 Systems have completed a more extensive refurbishment and improvement programme for 22 TCDA units to further extend the life of this excellent capability. This demonstrates the extreme robustness of the G3 Systems solution and the importance the Customer places on the quality and durability of the bespoke G3 Systems design. In addition to basic refurbishment and compliance work, this new programme of works includes the addition of a winterisation modification, to enhance the dog’s protection from the extremes of weather during winter months. This programme demonstrates excellent value for money for the tax-payer and ensures that those who help to protect us have the best possible facilities to operate in the most extremes of environments.
Nick Rose, Managing Director of G3 Systems said, “G3 Systems have a long history of providing high quality, robust and rapidly deployable containerised solutions to UK Defence, US DoD and UK Met Police and we are very proud of the fact that our work not only supports our troops (including working dogs) but also stands the test of time in the harshest of environments.”
Image caption: TCDA deployed in Afghanistan
G3 Systems: Helping to Pioneer NavyPODs Capability Development
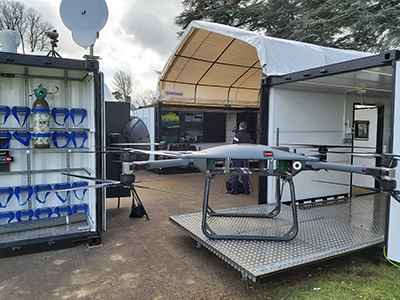
G3 Systems understands that in the ever-evolving landscape of naval warfare, innovation is paramount. One of the more innovative advancements for the Royal Navy in recent years has been the development of NavyPODs (Persistent Operational Deployment Systems) capability. At the forefront of helping pioneer this transformative concept was G3 Systems, a global leader in delivering deployable containerised solutions for defence and other government departments.
What are NavyPODs?
The Royal Navy’s vision for NavyPODs represented a paradigm shift in maritime capability. Rather than traditional ship designs with fixed systems, the focus switched to simplicity, adaptability, and modularity. The concept revolved around the idea of utilising PODs as standardised containers housing a spectrum of capabilities, ranging from precision strike and unmanned air systems to directed energy and medical aid. Inherent in the concept is the ability to re-role each POD as the requirement evolves.
By placing capability within PODs, that meet international freight standards, the fleet gained unparalleled flexibility, adaptability and maintainability to rapidly re-role platforms to meet the ever-changing demands of modern operational environments. Standardisation of components and modern digital networks enable rapid upgrades and easy interchangeability with allied forces. This approach not only enhanced lethality and sustainability but also offered significant cost savings and accelerated capability insertion periods.
NavyPODs embody a sustainable system designed to accommodate both current and future capabilities, aligning with the ambitious shipbuilding pipeline. The principle of ‘Pioneer, Prove, Procure, Plug and Play’ underscored the iterative development process aimed at swiftly delivering operational advantages.
G3 System’s history of containerised solutions
G3 Systems has a 20-year pedigree of delivering bespoke solutions to meet the specific needs of their customers and boasts a team of skilled engineers with a deep knowledge of engineering systems and technologies. From concept design to final implementation and through life support, they leverage their expertise to develop robust, reliable modular standardised deployable containerised solutions tailored to meet the unique requirements of the operational environments they may face.
Through experience developed in operational theatres such as Afghanistan, G3 Systems have become world leading experts in the integration of diverse payloads or capabilities into a cohesive system that is certified to international standards for safe transport and operation (Convention of Safe Containers). Their portfolio is vast with such innovative solutions as the Transportable Containerised Dog Accommodation (TCDA) and unique requirements of supporting the Foreign Office with deployable Embassies through to the development and delivery of the Navy’s Forward Support Unit concept. In addition, G3 Systems always considers the whole life aspect of their project. They excel in delivering a sustainable product that is easy to adapt as the requirement changes, simpler to maintain and repair by using standardised modular components and therefore minimises the logistic burden for the end user. With this approach, they have often been able to extend the life of a capability (such as the Deployable Engineering Workshop) with minimal upgrade far beyond its original design life.
Involvement in Navy PODs Development
G3 Systems adopts a proactive approach to project management, collaborating closely with Navy stakeholders to contribute innovative ideas and employing industry best practices to manage resources, mitigate risks and meet stringent deadlines. Combined with their expertise and commitment to excellence, this ensures successful outcomes for the client, even in the most challenging circumstances. As one example, for the Heavy Drone Lift capability, through such proactive approaches and excellent relations with key partners and the client, G3 Systems were able to support the rapid delivery of four systems in just 12 weeks. It has been proven through bitter experience that not all organisations possess the full gamut of capabilities required to successfully deliver a fully operational, high quality and robust containerised solution and therefore it is critical to maintain such capability within the UK’s industrial base to ensure operational effectiveness into the future.
G3 Systems contributions also extend far beyond technical implementation, encompassing training, technical support and full life sustainment activities. By empowering naval personnel with the knowledge and tools to effectively utilise PODs systems, G3 Systems helps maximise operational effectiveness and mission success which is often not a factor considered when selecting a contractor based purely on tender price. As a testament to the adaptability of the NavyPODs concept the PODs that G3 produced have also been used to cover such diverse requirements as a data visualisation environment, underwater vehicle and C2 planning centre and quantum technology test bed.
Looking to the Future
As maritime threats evolve and operational requirements change, the role of NavyPODs will continue to expand. G3 Systems remains at the forefront of this evolution, driving innovation and helping to shape the future of naval capability delivery systems. G3 Systems’ involvement in the development of NavyPODs capability underscores their position as a trusted partner in the defence industry. Through their engineering prowess, integration expertise and collaborative approach, they are helping to help redefine the way navies operate in the 21st century.
Image caption: Heavy Lift Drone Navy PODs produced by G3 Systems
G3 Systems wins overseas construction works contract for refurbishment of the British Deputy High Commission Office in Lagos, Nigeria
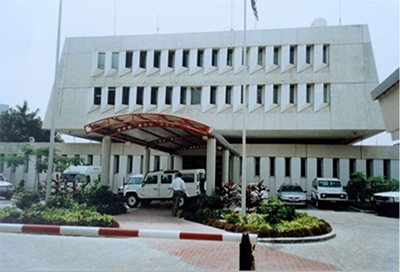
G3 Systems Limited, the British company with over 20 years of operationally proven expertise in designing and producing deployable containerised solutions and providing infrastructure support to military and government organisations in remote locations across the globe, has just been awarded a multi-million pound contract by the Foreign and Commonwealth Development Office (FCDO) for the remodelling and refurbishment of the British Deputy High Commission (BDHC) in Lagos, Nigeria.
The contract, awarded following a competitive tendering exercise, is a mix of demolition, refurbishment, new build and landscaping works estimated to take 18-24 months. The objectives of the FCDO project are to enhance the working environment for deployed staff, ensure compliance with modern building standards, maximise space utilisation and minimise ongoing maintenance and running costs.
The project will also seize the opportunity to enhance compound security and improve the compounds overall environmental performance, in line with government net carbon zero goals. Throughout the works, the BDHC will remain occupied and fully operational. Therefore, an essential component of the project is to provide close liaison with staff to ensure the project works are synchronised with their operational needs.
Nick Rose, Managing Director of G3 Systems said “This is excellent news for G3 Systems and a very exciting extension of our existing construction capability. We have a strong pedigree of providing deployable containerised embassy solutions for the government in the past and delivering projects in remote locations for the military, but this is a first to manage a complex construction project in a remote location for the FCDO, which is a fantastic addition to our current portfolio.”
Image caption: British Deputy High Commission Office in Lagos, Nigeria
G3 Systems extend the life of the British Army’s Deployable Engineering Workshops

G3 Systems has recently announced a rolling refurbishment programme to extend the life of the Deployable Engineering Workshops (DEW) capability for up to 10 years, whilst at the same time improving the DEWs overall performance to increase its sustainability and operational longevity.
The DEW system was first designed, developed and delivered into service in 2006 by G3 Systems, and the capability has stood the test of time having been used extensively on deployed operations around the world, including extended service in Afghanistan. The DEW comprises of twelve containers, along with a tented system, that provides a deployable engineering facility used by the military, and specifically the Royal Engineers, in theatre and for operational duties in both the UK and overseas. There are three remaining systems, which are used on a rotational basis dependent on operational needs.
Currently, one system is held in high readiness for deployment so for example could be used for the UK’s commitment to the NATO’s Very High Readiness Joint Task Force (VJTF). If tasked, this would be a key engineering capability required to support the high readiness brigade, along with other combat support and combat service support units such as the artillery, logistics and medical regiments. Another is deployed at Kinloss supporting current operations, leaving the third available to undergo the detailed life extension programme by G3 Systems at their integration facility in Weymouth.
The refurbishment programme is designed to extend the life of the capability by 10 years, ensure compliance with current electrical regulations, maximise the performance of the DEW and minimise its environmental impact. For example, G3 Systems will be employing smart technologies to reduce the power utilisation of the DEW, thus enhancing the working environment and reducing the DEW’s overall carbon footprint.
Nick Rose, Managing Director of G3 Systems said “we were very proud of the DEW when it was first deployed and have remained engaged with the programme throughout its operational life. This programme is an excellent opportunity to extend the life of this superb capability. It also demonstrates how industry, and the military, can work together to deliver multi-faceted solutions, save taxpayers money and improve sustainability; while still delivering military capability for front line operations.”
Mike Batty Head of Operational Infrastructure for DE&S said, “The Deployable Engineering Workshop is vital to supporting successful operations and I am delighted that we have ensured this unique capability for the British military is available for years to come.”
Image caption: DEW in G3 Systems Integration Facility, Weymouth
G3 Systems reshapes it leadership to prepare for the future
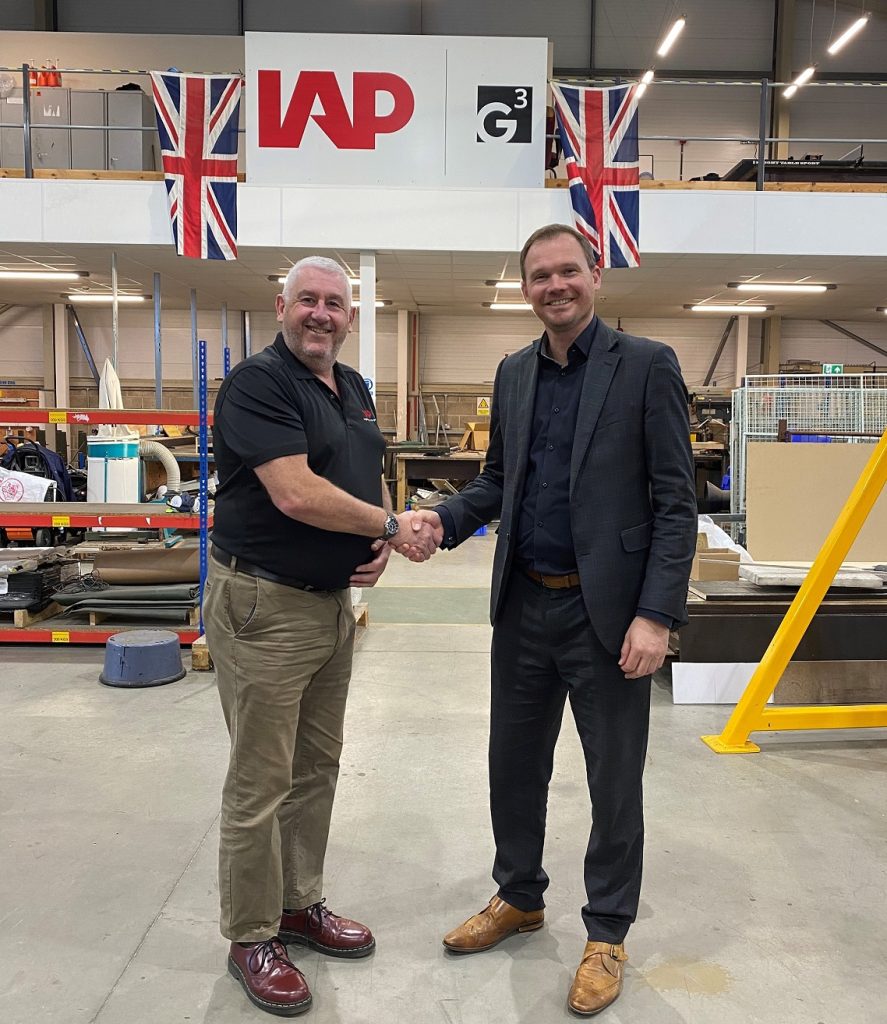
G3 Systems Limited, the British company with over 20 years of operationally proven expertise in designing and producing deployable containerised solutions and providing infrastructure support to military in remote locations across the globe, is reshaping its senior leadership to meet the future demands of the business.
Under the leadership of Mike Puckett, G3 Systems had updated its strategy and revised its operational delivery model to better meet future client needs and the appointment of Nick Rose as the new Managing Director was the final component of this plan. Mike Puckett will continue to support the growth of the business in an advisory capacity.
Nick Rose is no stranger to G3 Systems, having recently reached his 15 years’ service milestone. During his tenure, he has honed his leadership skills from leading the HR department to more recently being the Business Support Director with responsibility for IT, administration and finance and so is well placed to lead the business into the next era.
The future for G3 Systems is looking very exciting, with opportunities in all sectors of their business. They are looking forward to the opportunity to be able to report on their recent successes across the key areas of ESS, Support Services and their construction arm, plus a return to Rescue and Fire Services.
Mike Puckett said, “I am extremely grateful to the team at G3 Systems Limited for their support and dedication as we transitioned through a time of withdrawal from Afghanistan and surviving the COVID Pandemic. The business strained but we have come out fighting, and in a position of strength going forward.”
Nick Rose, new Managing Director said, “I am delighted to have the backing of IAP management in my appointment as MD. I am totally committed to G3 Systems, and I am as enthusiastic as ever about the organisation. I am very proud to come to work each day and work with the team to drive the business forward and ensure every client speaks highly of the products and services we deliver.”
G3 Systems and Utilis deliver 2nd Role 2 Field Hospital for the Belgian MOD, September 2023
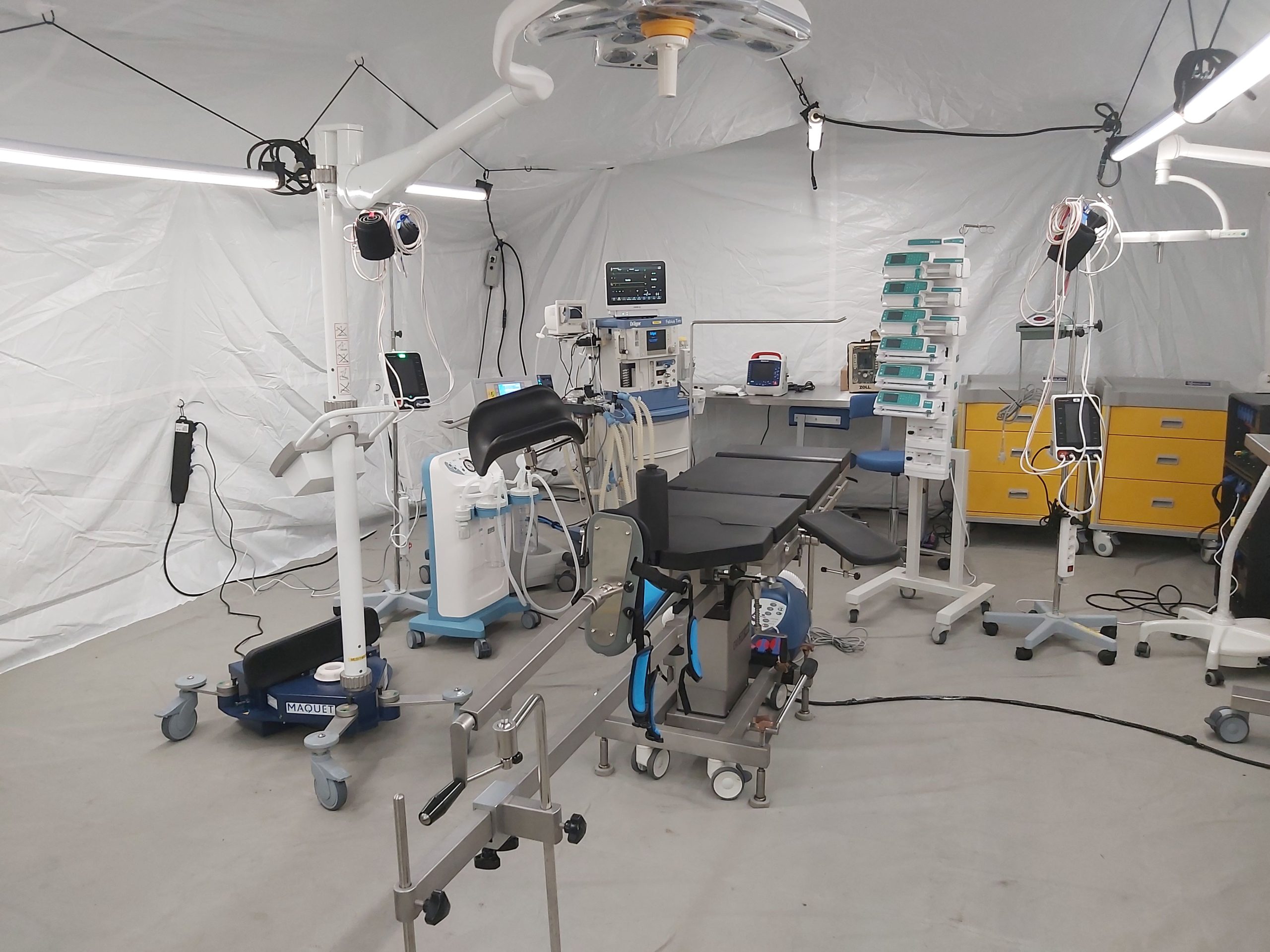
G3 Systems Limited, the British company with over 20 years of operationally proven expertise in designing and producing deployable containerised solutions and providing infrastructure support to military in remote locations across the globe, has delivered in partnership with Utilis a second fully deployable Role 2 Field Hospital. The G3 Systems team will be at DSEi23 available for meetings to discuss similar deployable infrastructure solutions and all their other infrastructure support capabilities.
G3 Systems were invited to form a partnership with Utilis to maximise their respective skills and experience in the deployable infrastructure sector to bid for the contract in 2020. Both companies have a strong operational pedigree with metallo-textile structure solutions, rapidly deployable infrastructure and supporting military operations in austere locations. For this contract, Utilis led on the delivery of the tents, shelters and M&E infrastructure while G3 Systems were responsible for delivering the medical equipment and providing the through life support. The G3 Systems – Utilis partnership was successful in bidding for the contract in 2020 and together, through the most challenging pandemic era, they delivered the first of two Role 2 Hospitals in December 2021. Subsequently, the option of an order for a second Role 2 Hospital was received in 2022 for which Initial Operating Capability (IOC) was achieved in April this year and a target date of Full Operating Capability (FOC) for the whole contract is expected by 2026.
A Role 2 Field Hospital is a vital element in the medical evacuation chain as it is deployed forward in a conflict zone to minimise the time taken from injury to primary treatment. Its mission is to identify, triage, and if necessary, operate on casualties to stabilise them before they are transported to more specialist care or rehabilitation further from the conflict zone. The G3 Systems – Utilis solution meets the demanding military specifications imposed by the Belgian MoD and the shelters have successfully passed rigorous testing to NATO standards including in extreme weather conditions. These factors combined with the speed and ease of deployment ensures that the Belgian MoD can fully deliver on their NATO medical support commitments.
Nick Rose, Managing Director at G3 Systems Limited said, “Both G3 Systems and Utilis have vast experience in this sector and this project is an excellent example of true partnership working to deliver the best possible capability for the client. I am also delighted with how the project has progressed through some significant global challenges and wish to commend all the project team for their tireless commitment and professionalism to overcome such hurdles and still deliver an excellent product for our customer.”
G3 Systems deliver unique Fire Trials & Evaluation Unit for the Royal Navy at Horsea Island, June 2023
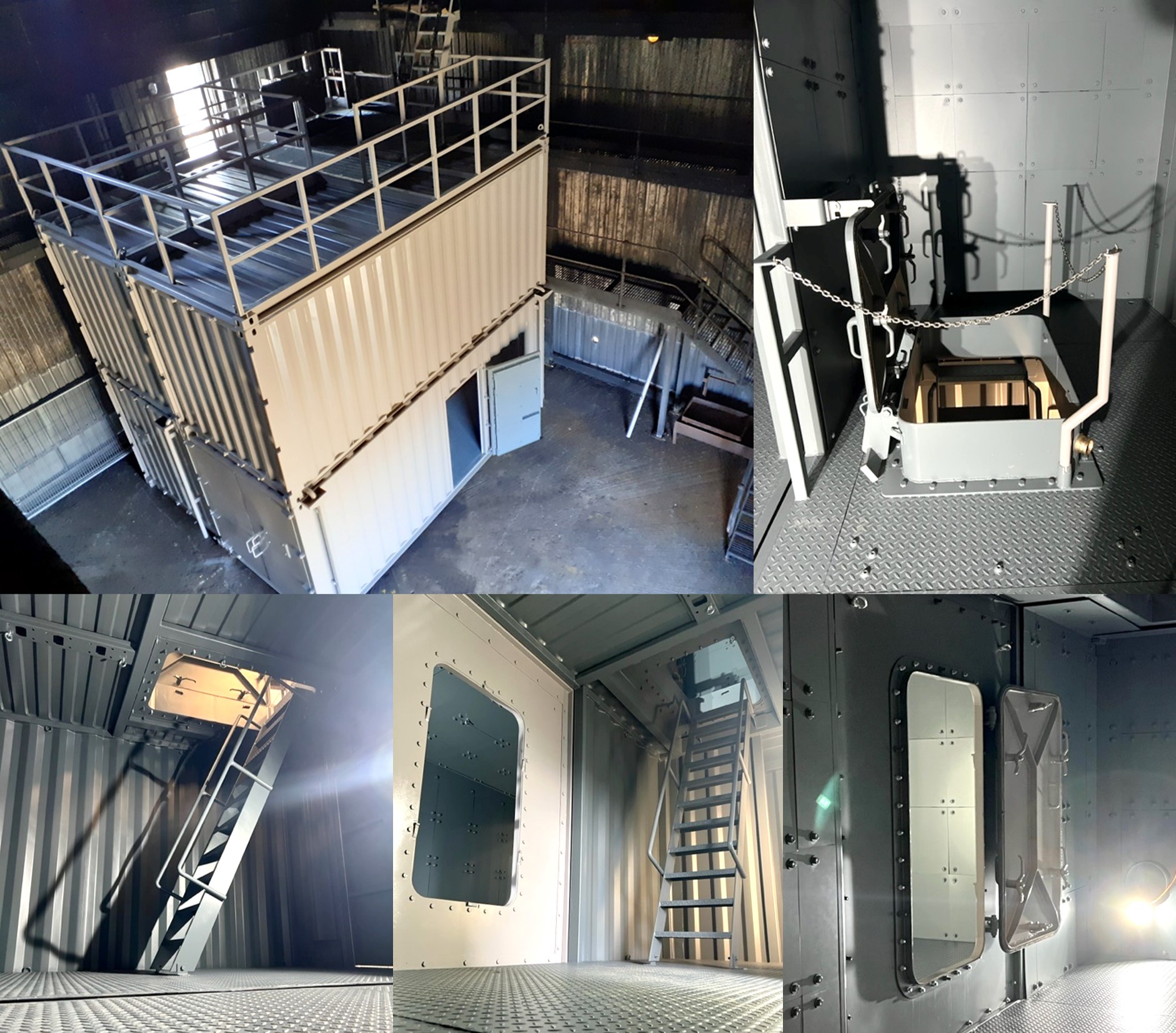
G3 Systems Limited, the British company with over 20 years of operationally proven pedigree in designing and producing deployable containerised solutions, has delivered a specially designed and constructed Fire Trials and Evaluation Unit (FTEU) for the Royal Navy at Horsea Island.
The FTEU allows realistic simulation of fire behaviour within MOD vessels by conducting live fire testing and equipment analysis on behalf of Navy Command Head Quarters (NCHQ) and Defence Equipment and Support (DE&S) / Submarine Delivery Agency (SDA) Equipment teams and Platform Authorities. The valuable data and experiences gained through the trials facility inform equipment selection and develop firefighting policy, procedures, and techniques, conducted in a controlled environment, before becoming Royal Naval policy.
G3 Systems Limited, a wholly owned subsidiary of IAP WWS Inc, has a long history of producing modular, deployable containerised solutions for the Royal Navy (Forward Support Units and more recently NavyPODs for the heavy lift drone capability). For this project, they had to combine three key elements of unique capability and experience to meet the customers demanding requirements; previous research in fire propagation and risk in containerised units, operational fire-fighting experience gained from providing fire and rescue services in Afghanistan and their long history of producing bespoke containerised solutions for defence and other governmental organisations.
The output is the unique FTEU which, is modular by design, and built to fit into the existing available floor plate with minimal changes to infrastructure, utilising existing supplies and discharge routes but incorporating safety and functional improvements when compared to the old FTEU facility. The burn unit is designed to be safely operated with a minimum of two personnel but with the ability to flex to five personnel in full firefighting equipment, including breathing apparatus, transiting through at any time. The system is designed to minimise risks to personnel during operation and maintenance, taking into account the latest fire safety legislation whilst providing a valid representation of a Naval environment.
Mike Puckett, Managing Director at G3 Systems Limited said, “G3 Systems are world renowned for producing deployable containerised solutions, but less well known for our facilities management or fire-fighting services. This project is an excellent example of the depth of experience that G3 Systems possesses, and it is extremely rewarding to design and deliver such a unique capability drawing on every element of our business.”
Lieutenant Commander David Cummings, RN said: “The installation and commissioning of the new Fire Trials and Evaluation Unit has now restored the capability of the Royal Navy to carry out live fire trials, which are specific to RN ships and platforms. Trials and results are invaluable in shaping future RN firefighting policy and equipment procurement. We are content G3 have successfully delivered a design which is not only marine applicable, but also adaptable to allow a versatile range of future trials to be conducted. The unit will ensure the RN can again move forward and continue to develop on board firefighting for the foreseeable future.”
IAP CEO Terry DeRosa: Chamois Interview, November 2022
G3 Systems Limited is a wholly owned subsidiary of IAP Worldwide Services Incorporated. Last week the CEO (Terry DeRosa) and COO (Rob Hargis) visited G3 Systems to review performance, visit the integration facility and discuss strategy for a host of future opportunities. During the visit, the IAP team met with our communications consultants (Chamois) and Terry spoke to their Director of Media and PR (Gareth Baker) about the benefits to G3 Systems customers of having IAP as a parent company – scale and reach back expertise – and the key capabilities G3 Systems provides for IAP – rapidly deployable operational solutions. The week was a great success and timely as the new Navy Pods invitation to tender is released, we are expecting a follow-on order of deployable containerised solutions from a local company, and we have bids submitted or are preparing for bids in the African and South Atlantic regions.
G3 Systems article in The Catalyst
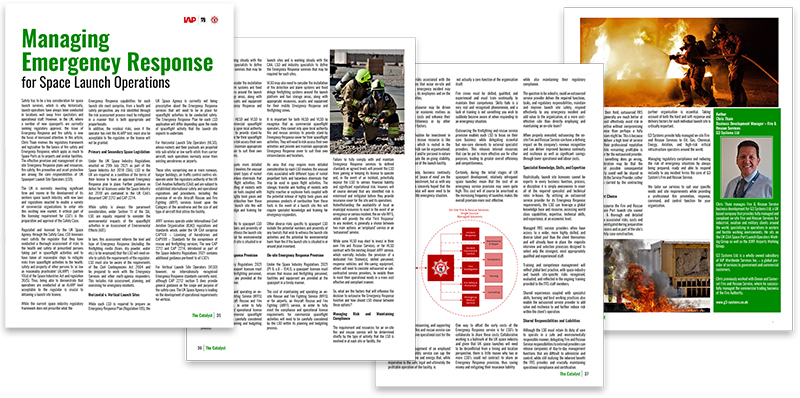
G3 Systems Business Development Manager Chris Thain talks about managing emergency response. Click here to read the full article.
G3 Systems Delivers four NavyPODS (Deployable Containerised Solutions) for Heavy-Lift Drone capability in Record Time
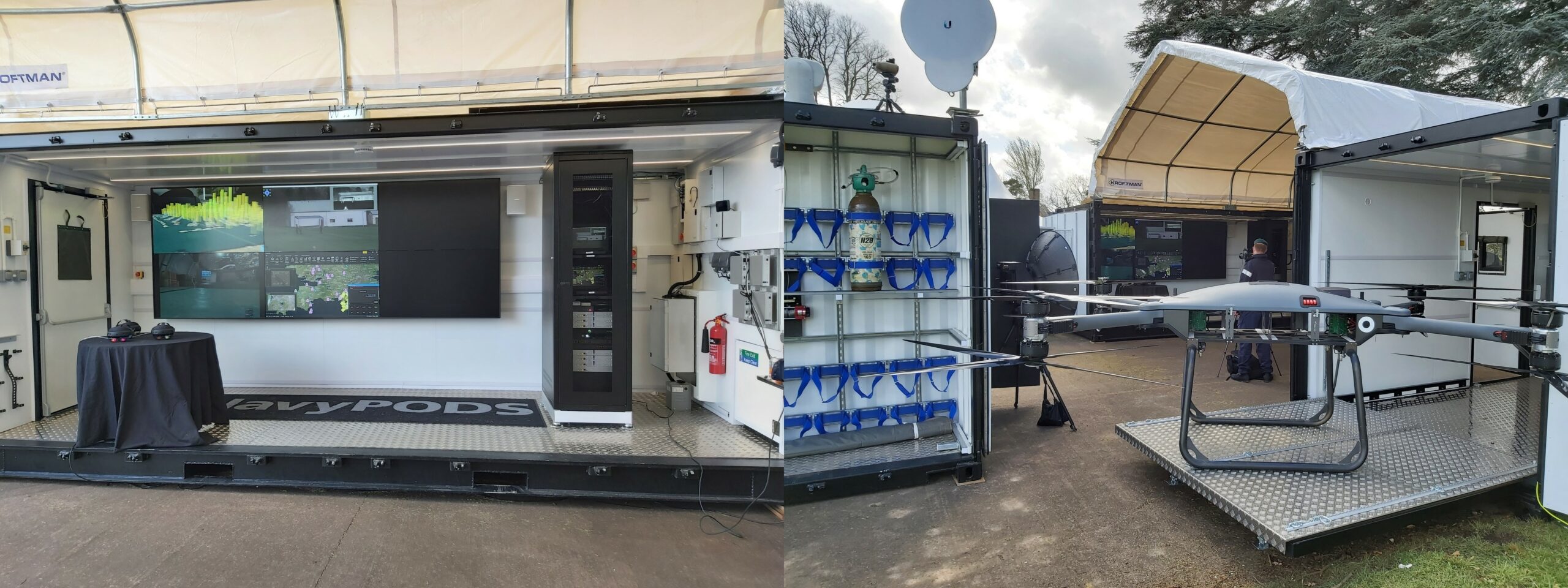
G3 Systems Limited has – working with QinetiQ – delivered four systems (deployable containerised solutions) to support the Royal Navy Persistent Operational Deployable Systems (NavyPODS) required to transport and control the new heavy-lift drone capability in a record time of 12 weeks. G3 Systems will be available at DVD 22 to discuss this project, and all their capabilities, on stand C4-401, at UTAC Millbrook, Bedfordshire 21/22 September 2022.
G3 Systems Limited, a wholly owned subsidiary of IAP WWS Inc., has over 20 years of operationally proven history in designing and building deployable containerised solutions, delivering critical operational infrastructure and providing facilities support in austere locations. NavyPODS are interchangeable modules that can be fitted to the surface fleet. Using a shipping container as the transport medium, NavyPODS deliver the concept of a ‘plug and play’ warship and enable Royal Navy ships of all sizes to be more adaptable and versatile when deployed. By combining NavyPODS and surface platforms, greater operational effect will be achieved by being interchangeable, interconnected and integrated allowing the Royal Navy to rapidly respond to a variety of taskings. The heavy-lift drone capability is a key building block of this concept and G3 Systems provided the deployable containerised solution to transport, control and maintain these drones.
G3 Systems have vast experience and expertise is designing, building and supporting such high specification, bespoke, deployable containerised solutions. This project required all the ingenuity, agility and purpose G3 Systems are famous for, to work closely with the customer, QinetiQ and various suppliers to integrate the rapidly changing requirements and still deliver against such short timelines. A normal project of this scale would take 16 to 20 weeks, but by drawing on past experience, standardised proven solutions and the knowledge gained during the Royal Navy Forward Support Units (FSU) refurbishment programme, it was possible to deliver all four systems with three separate designs within 12 weeks, which is a new record for G3 Systems on such a complex project. It clearly demonstrates G3 System’s flexible and agile approach to design, and their ability to quickly ramp up capacity to meet challenging deadlines.
Mike Puckett, Managing Director at G3 Systems Limited said, “We are very pleased with the outcome of this exciting project with the Royal Navy. Over 20 years we have become experts in designing and building complex containerised solutions, and the Royal Navy has seized on this concept for both FSUs and PODs to maximise their flexibility and response time. I am very proud of the G3 team that we were able to mirror this concept and deliver a high-quality sustainable, flexible product in record time.”
G3 Systems Launch a Refreshed Strategic Plan
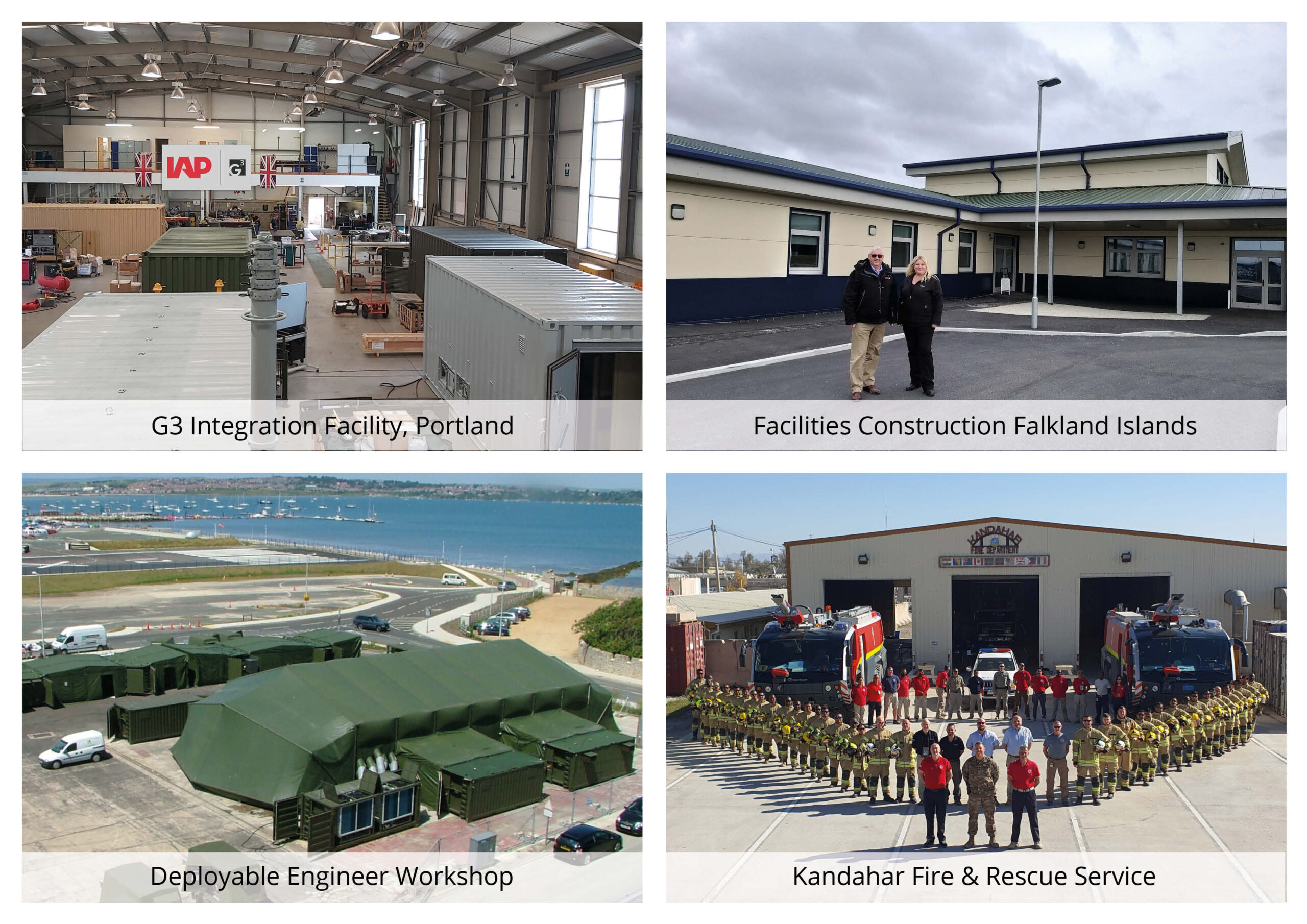
G3 Systems Limited, the world-renowned provider of bespoke deployable containerised solutions, critical operational infrastructure and facilities support in austere locations has launched its refreshed 3-year Strategic Plan. The plan focuses on identifying areas for growth and diversification and seeks to promote core functions and capabilities to new clients and geographies; whilst capitalising on recent operational experience such as providing Fire and Rescue services in Afghanistan. The Plan also includes an increased focus on sustainability, environmental protection and social responsibility.
G3 Systems Limited, a wholly owned subsidiary of IAP WWS Inc., has launched its refreshed 3-year Strategic Plan stating their vision to be “dominant in the provision of bespoke high quality deployable and fixed infrastructure and a leader of support services in austere environments”. This vision is underpinned by their company ethos of Ingenuity – Agility – Purpose and built on four strategic pillars: a relentless focus on the demands of the Customer and delivering that with excellence; empowering People with learning and growth to foster a safe and sustainable environment; achieving internal and external operational quality and efficiency through rigorous Business Process and diligent stewardship of Finances to ensure excellent value for money.
G3 Systems Limited has a 20-year history and an operationally proven track record of delivering in the most challenging and arduous environments. They are proud of their company culture of achieving the ‘out of the ordinary’, going to challenging places and working ‘as one’ with their clients while never failing and always looking after the people and the environment around them. They have been integral to the success of many long-term operational deployments in Iraq, Afghanistan and the Falkland Islands. Their modular, standardised and highly adaptable solutions such as the Deployable Engineer Workshop, Navy Forward Support Units and FCO Deployable Embassy have been and will continue to be excellent solutions to meet the needs of rapidly deployed government and non-government organisations.
Chamois Consulting Limited has also been engaged to assist G3 Systems Limited in the delivery of their strategy. They will be providing a particular focus on brand communications, client and stakeholder engagement and to help raise the social awareness of G3 Systems Limited products and services.
Mike Puckett, Managing Director at G3 Systems Limited said, “I am very proud of the G3 team and the significant progress we’ve made to date. Following a change in the nature of deployed operations, and through the refreshed strategy process, we’ve recognised that it is time to build on our social value interfaces, external communications, marketing and adopting new methods to enhance our collaborative working and to help share our vision and achieve our strategic goals. Having seen what has been achieved with other defence orientated companies, Chamois was the natural choice and I am really looking forward to working with them.”
Gareth Baker, Director of Media and PR at Chamois said “I am really excited to be working with G3 Systems Limited, because I was already sighted on some of their products from my time on operations. However, prior to spending time with the team, I had no idea of the depth, breadth and scale of their skill, operational pedigree and engineering expertise. I am very much looking forward to helping communicate their substantial capabilities to their target audiences.”
G3 Systems article in International Fire & Safety Journal
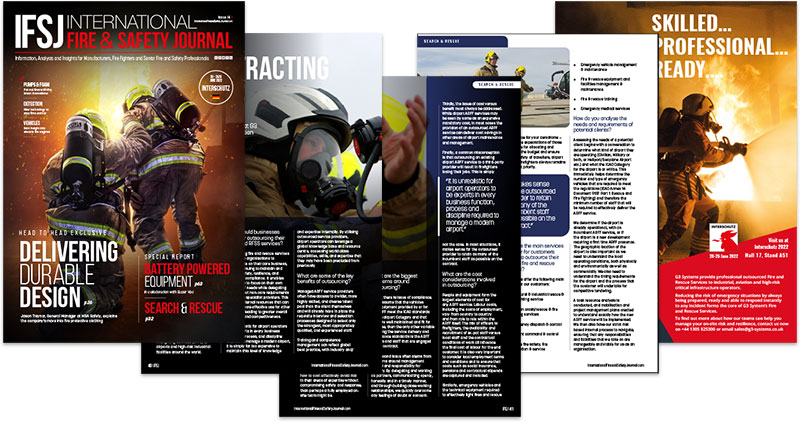
G3 Systems Business Development Manager Chris Thain talks outsourcing aviation fire and rescue services. Click here to read the full article.
G3 Systems awarded Cyber Essentials Plus certification
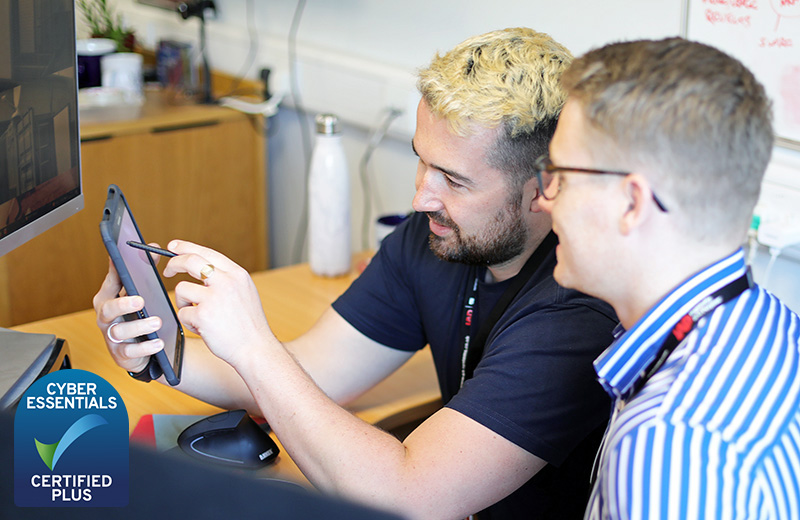
Cyber Essentials is a UK government-backed framework scheme created in 2014 and supported by the National Cyber Security Centre (NCSC). The scheme is designed for all organisations as cyber-attacks can impact businesses of all sizes, industries, and sectors and sets out five basic security controls that can protect organisations against 80% of common cyber-attacks.
Cyber-attacks are increasing both in frequency and sophistication. Achieving Cyber Essentials Plus shows G3 Systems commitment to reducing the risk of IT security breaches. Very few organisations have achieved this important accreditation, which places G3 Systems at the top of the defence manufacturing sector regarding information technology and Cyber security.
Surprisingly, most cyber-attacks are usually carried out by an individual attempting to breach the information system of another organisation, using five primary methods. The basic self-assessed Cyber Essentials scheme details the five security controls designed to prevent cyber-attacks and guard the organisations internet connection, devices, data, and services. These controls include boundary firewalls, secure system configuration, control user access, patch control, anti-malware, and phishing protection.
Cyber Essentials PLUS has the same control requirements as Cyber Essentials, however, the critical difference is that Cyber Essentials PLUS also requires an on-site security vulnerability assessment by an experienced independent IT security consultant, which included a stringent 2 -day IT audit at G3 Systems headquarters in Portland, Dorset, UK.
The security testing at G3 Systems covers all Internet gateways, all servers providing services directly to unauthenticated Internet-based users and representative sampling of devices that connect to the Internet. This ensures that security measures are operating properly and are sufficient in protecting cyber threats against the company.
The Cyber Essentials Plus accreditation will bring many benefits to G3 Systems, including greater protection against the most common cyber-attacks, an increased trust, credibility and reputation with stakeholders and notably new business opportunities with our Government and Defence sector clients.
NEWS: G3 Systems exhibiting at Interschutz 2022
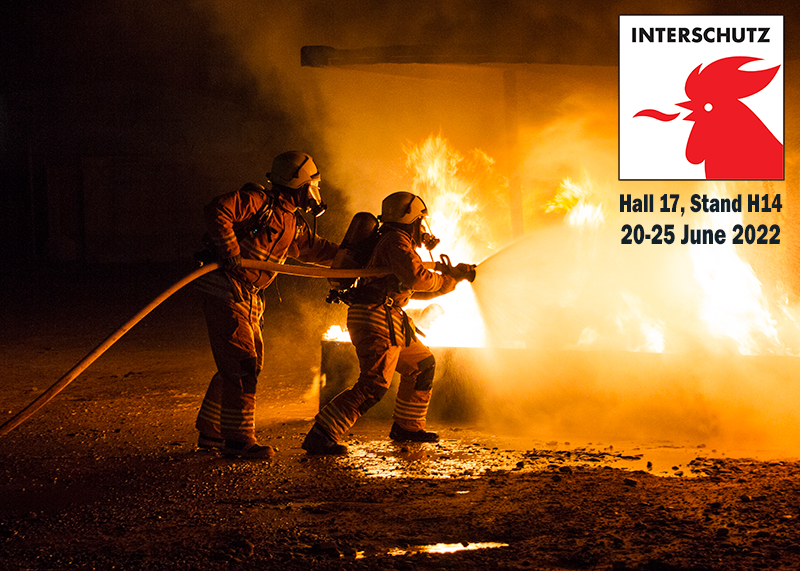
G3 Systems Limited is pleased to announce that it will be exhibiting at Interschutz 2022, the world’s foremost fire, rescue, civil protection, and safety/security trade show, from June 20-25, 2022, at the Deutsche Messe Hannover, Germany. Interschutz was last held in 2015, however the show was sadly postponed in both 2020 and 2021 due to the global Coronavirus pandemic.
Joining around 1000 other companies from 50 countries, G3 Systems will be presenting its outsourced fire and rescue service capability to industrial, aviation and critical infrastructure customers from around the world.
With around 160,000 visitors expected to visit the show over 6 days, G3 Systems will demonstrate how its 24/7 Fire and Rescue Services can minimise risk and improve on-site safety; protecting staff, visitors and facilities while enabling operations to continue in full compliance with national and international fire and safety standards and regulations.
Based in Portland UK, and currently celebrating 20 years in business, G3 Systems is a market leading provider of outsourced fire and rescue services, engineering & service solutions covering deployable and fixed infrastructure and systems, and support services.
G3 Systems Fire & Rescue Services include structural and aviation rescue and fire-fighting services, emergency dispatch and response, incident command, fire safety, fire inspection and investigation, equipment and vehicle maintenance, testing and compliance, firefighter training and Medical Crash Crew / Ambulance Services. In addition, G3 Systems provide waking watch services and client training in emergency response procedures, as well as through-life logistics support via mobile Field Service Engineers and forward deployed support staff. Over 80% of its personnel work at its client’s facilities around the world.
If you are attending Interschutz 2022, G3 Systems cordially invites you to Stand H14: Hall 17, where Chris Thain, Business Development Manager – Fire and Rescue Services and other G3 Systems staff will be on hand to discuss your emergency response and resilience requirements.
NEWS: G3 Systems supports Helicopter Search and Rescue services in the Falkland Islands
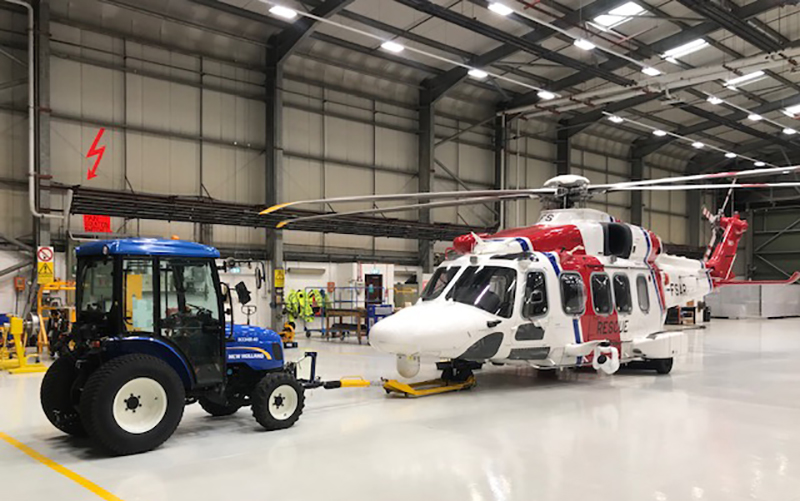
G3 Systems has recently completed its first field service visit to British International Helicopters (BIH) at Mount Pleasant Airfield in the Falkland Islands. The purpose of the visit was to provide condition assessment surveys and servicing of essential Ground Support Equipment (GSE) for two Search and Rescue (SAR) Helicopters based on the Islands.
BIH, the largest UK-owned helicopter operator, works on behalf of the UK MOD’s Defence Equipment and Support department to provide search and rescue support to the British Forces South Atlantic Islands operations. BIH operates two AW189s in the Search and Rescue role and two S61N Support Helicopters on the Islands.
The SAR service is operational 24 hours a day, 365 days a year and carries out all-weather search and rescue, helicopter emergency medical services, rescue hoist operations, passenger and cargo transfers and night vision imaging, in extremely challenging environmental conditions. The Support Helicopter Service provides the military garrison with helicopter transportation of both personnel and equipment throughout the Islands.
Maintenance, logistics and operations for the Helicopters are managed by BIH, who contracted G3 Systems to provide on-site field-based maintenance and servicing support for the GSE. G3 Systems conducted a condition assessment of each piece of equipment before undertaking a full service as part of the equipment maintenance scheduling.
Tools and necessary spare parts were shipped to the Falkland Islands prior to the departure of the G3 Systems Field Service Engineer. Upon arrival and after completing a mandatory CV-19 quarantine, the G3 Systems Engineer set about locating, assessing, and servicing the equipment in accordance with the OEM’s approved technical manuals. The GSE includes three New Holland tractors, towbars, Ground Power Units and testing systems, hydraulic jacks and pumps, pressure washers, diesel generators, air compressors, and hangar floor scrubbers.
A servicing schedule has now been developed and agreed with BIH, and further visits are planned to maintain the operational effectiveness and safety of the GSE in the future.”
Image Caption: Falkland Island Search and Rescue (SAR) capability provided by BIH with Ground Support Equipment serviced by G3 Systems.
NEWS: G3 Systems article in Emergency Services Times
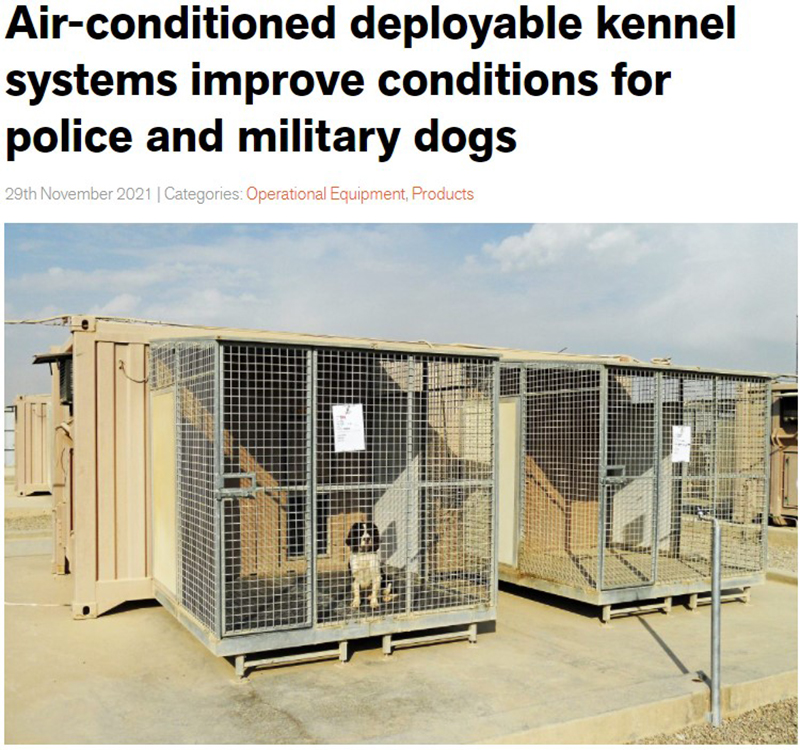
Specially constructed deployable dog kennels have been designed by G3 Systems Ltd to improve the living conditions for law enforcement and military working dogs.
To access the full article please click on the logo below.
NEWS: G3 Systems enhances the Royal Navy’s Forward Support Unit
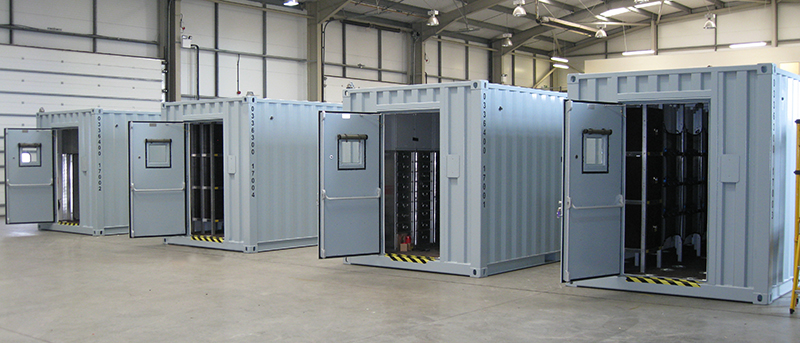
G3 Systems has recently completed a successful 5-year programme for enhancing the Royal Navy’s Forward Support Unit (FSU).
Currently situated at HMS Jufair in Bahrain, the FSU’s Containerised Engineering Support Facility (CESF) systems are designed to offer deployable, modular container systems that provide storage and engineering facilities to conduct Level 2 maintenance supporting the availability of the Royal Navy’s Mine Counter Measures Vessel (MCMV) fleet.
Support Mine counter measures
The role of the MCMV fleet is to search the world’s seabeds for mines and lost explosives which are then destroyed by the ship’s clearance diving teams or its SeaFox Mine Disposal System. The vessels’ sonars are capable of detecting and classifying an object the size of a football at depths of up to 1,000 metres.
Deployable Containerised Engineering Support Facilities
While operating in UK and foreign waters, the current UK fleet, consisting of six Hunt class MCMV and five Sandown class Mine Hunter vessels, is supported by two CESF systems designated CESF 01 and CESF 02.
Each system is comprised of a set of containerised workshops, offices and stores which can be independently powered by a single Power Generation Module (PGM).
Each module is designed so that it can be rapidly deployed by either land, sea or air and must be fully certified under the Convention for Safe Containers (CSC) and for flight by the MOD’s Joint Air Delivery Test and Evaluation Unit (JADTEU).
Each FSU CESF comprises up to 20 specialised containers including stores, workshops, offices, combination units and power generation, with units including communications, ablutions, electrical maintenance, shipwrights workshops, small arms management, a light machine shop, refrigeration and a lifting and slinging store. The units also contain first aid and safety equipment including a first aid kit, eyewash and fire extinguishers.
Cost savings, life extension and regulatory compliance
The objective of the G3 Systems programme was to extend the life of the CESF systems, ensuring full legislative and regulatory compliance and enhancing the safety of the facility. Through the improvements and standardisation of CESF equipment and components, G3 Systems were able to reduce maintenance costs and improve management of the support logistics, enabling further savings to be made.
Nick Broom, G3 Systems’ Operations Director, commented “We have enjoyed a close working relationship with the RN FSU over the past 5 years and are proud of the CESF systems we have delivered. The CESF systems provide a modular, deployable capability that can be adapted to a broad range of operational requirements and we look forward to working with the RN to develop their future capability through programmes such as NavyPODS.”
Image Caption: The Royal Navy’s Forward Support Unit (FSU) after complete refurbishment at G3 Systems integration facility at Portland, Dorset, UK.
NEWS: G3 Systems article in ROOM Space Journal
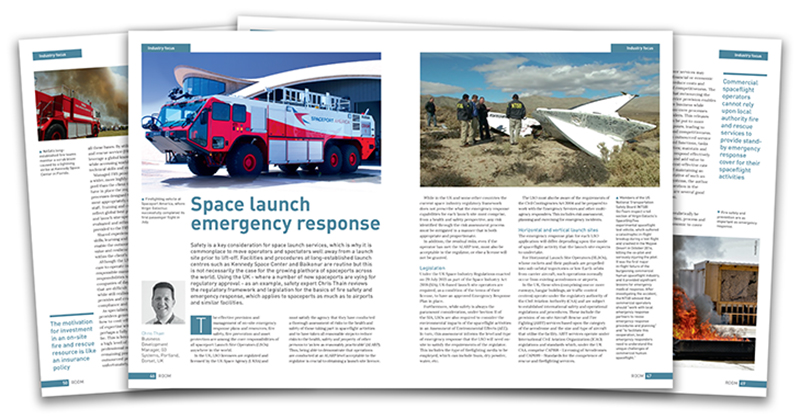
G3 Systems Business Development Manager Chris Thain reviews the regulatory framework and legislation for the basics of fire safety and emergency response, which applies to spaceports as much as to airports and similar facilities.
To access the full article please click on the logo below.
NEWS: G3 Systems article in Advance magazine
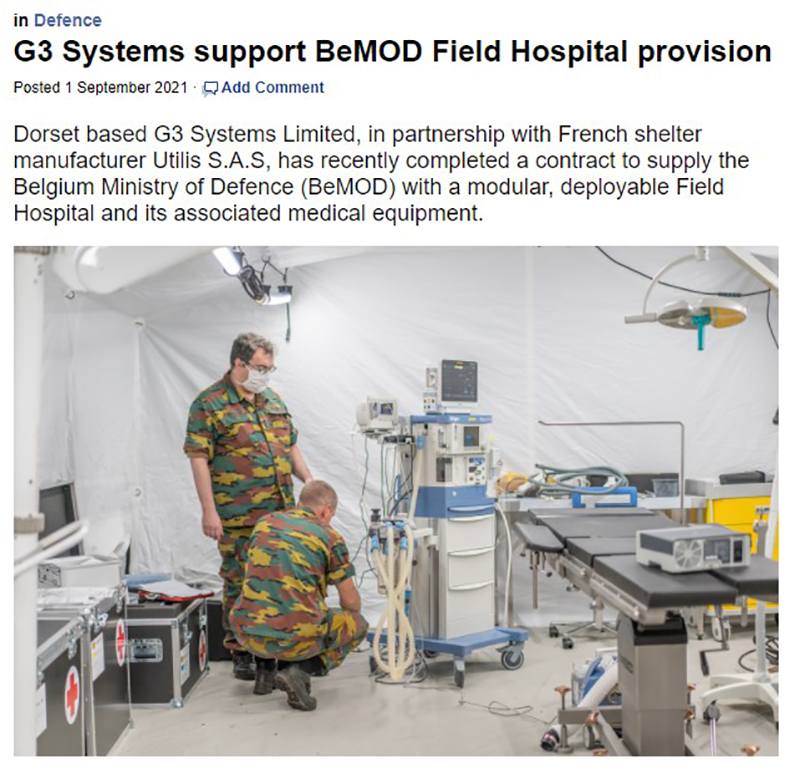
The article talks of G3 Systems involvement in BeMOD Field Hospital.
To access the full article please click on the logo below.
G3 Systems article in International Fire Fighter magazine
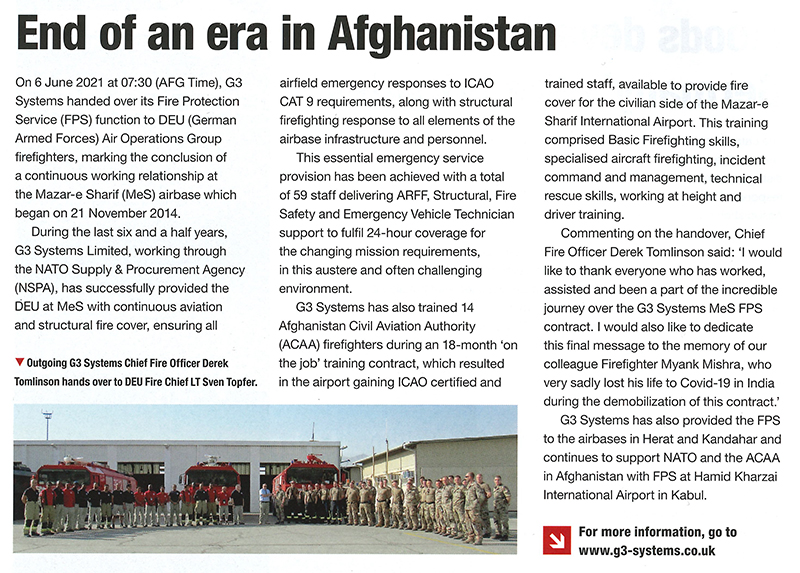
An article in International Fire Fighter on G3 Systems Fire Team last few days in Mazar-e-Sharif, Afghanistan.
Armed Forces Covenant Silver Award
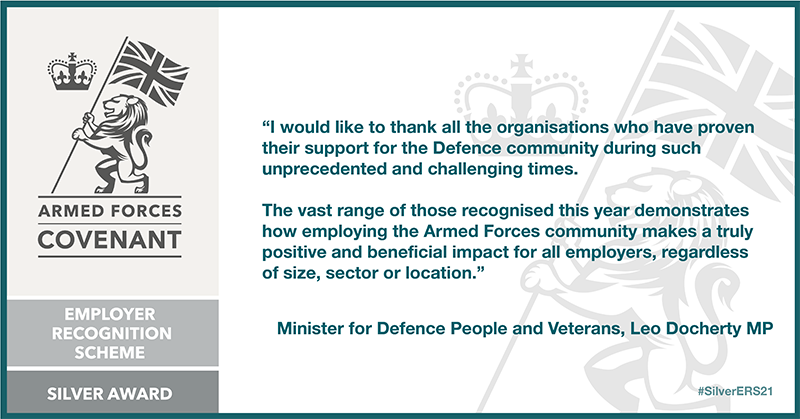
G3 Systems Ltd is delighted to have revalidated its Silver Award under the Armed Forces Covenant Employer Recognition Scheme. As a long standing defence contractor, celebrating our 20th Anniversary in 2021, we are proud of the support we have provided to the nation’s armed forces at home and abroad throughout the past two decades and through our employment of veterans, who make up around 35% of our work force. We strongly believe in the value that veterans bring and look forward to continuing to support the aims of the Armed Forces Covenant.
G3 Systems article in Asia Pacific magazine
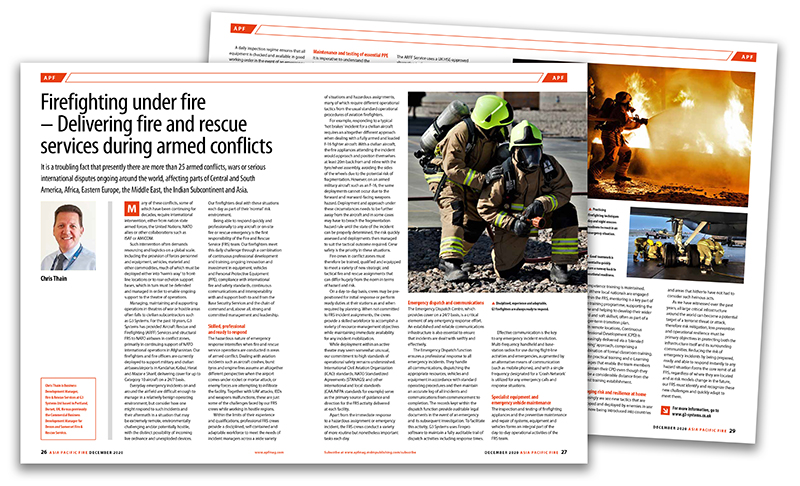
This feature article in Asia Pacific Fire magazine studies how Fire and Rescue Services can be delivered during periods of armed conflict.
To access the full article please click on the logo below.
G3 Systems article in UK Fire magazine
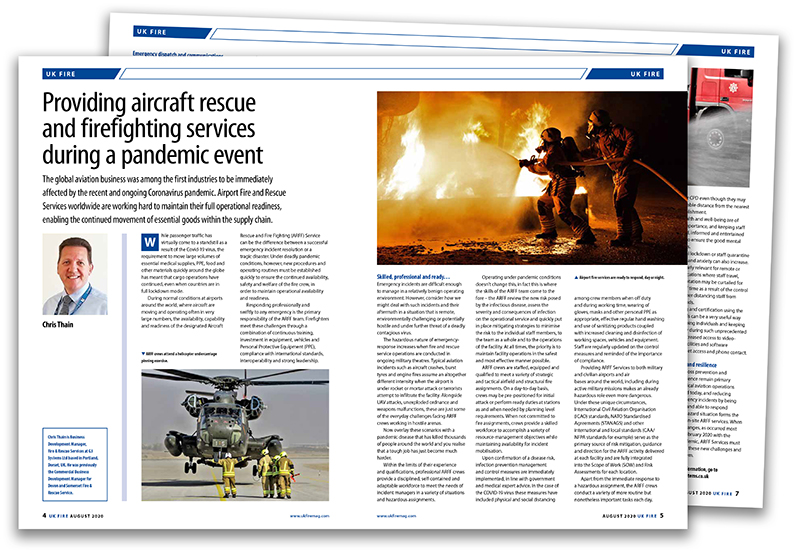
This feature article in UK Fire magazine considers how G3 Systems have provided ARFF services through the global pandemic.
To access the full article please click on the logo below.
G3 Systems article in Fire Tribune magazine
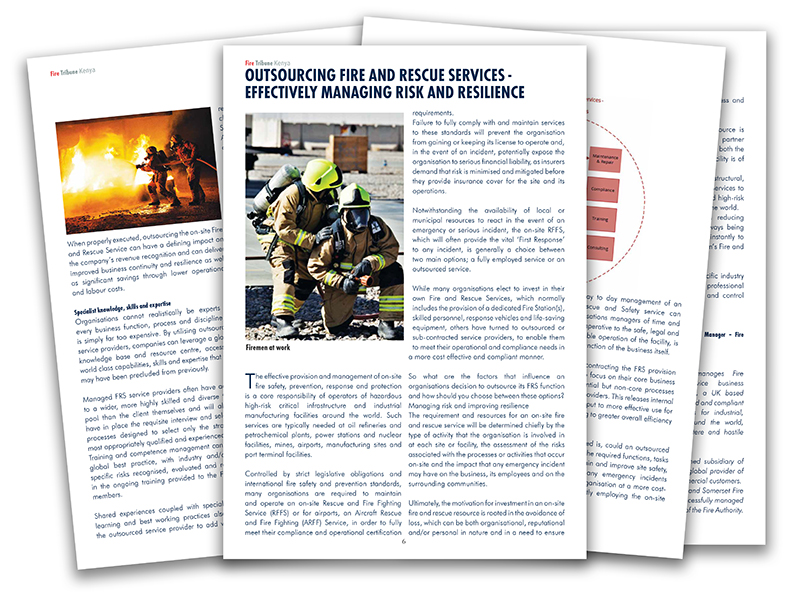
This feature article in the Fire Tribune magazine examines the benefits and implications of outsourcing on-site industrial firefighting services.
To access the full article please click on the logo below. Article on pages 8-11.
G3 Systems article in Gulf Fire magazine
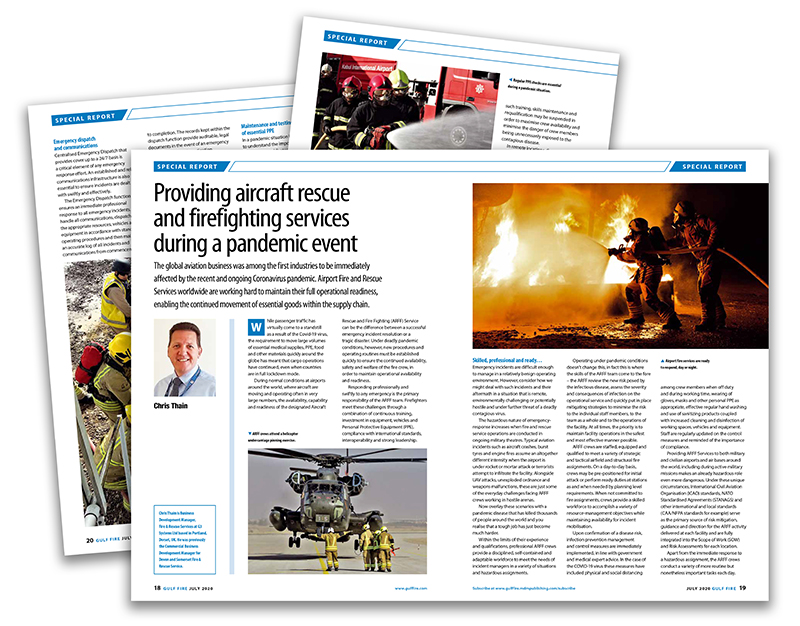
This feature article in Gulf Fire magazine investigates how G3 Systems have provided ARFF services through the global pandemic.
To access the full article please click on the logo below.
G3 Systems article in JOIFF Catalyst magazine
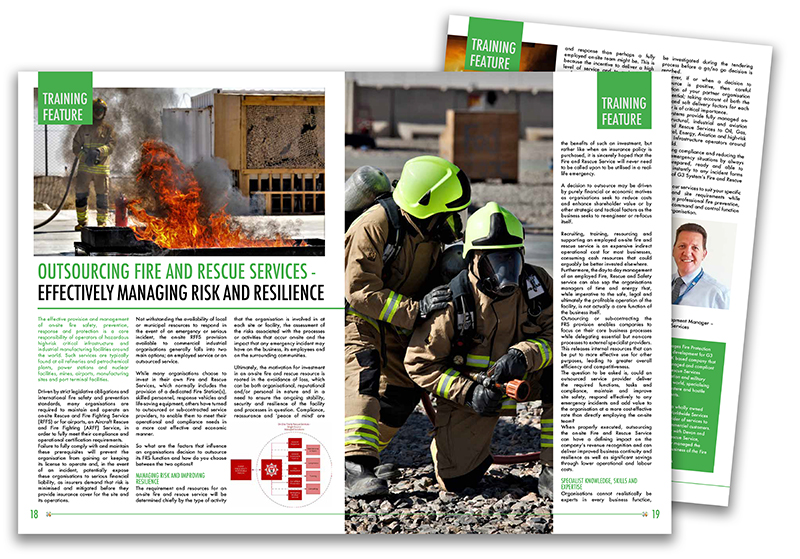
This feature article in the JOIFF Catalyst magazine examines the benefits and implications of outsourcing on-site industrial firefighting services.
To access the full article (Pages 18-20) please click on the logo below.
G3 Systems article in the International Fire Fighter magazine
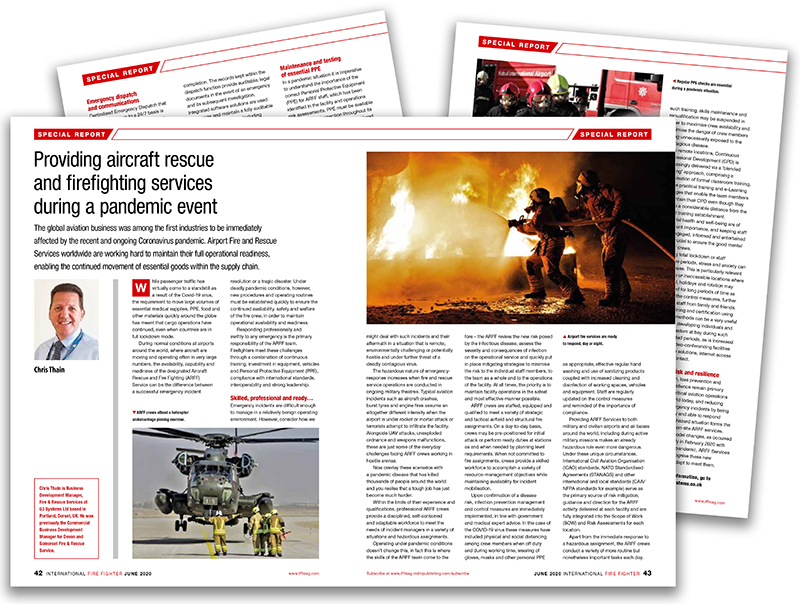
This feature article in International Fire Fighter magazine looks at how G3 Systems have provided ARFF services through the global pandemic.
To access the full article please click on the logo below.
Welfare Packages for Afghanistan
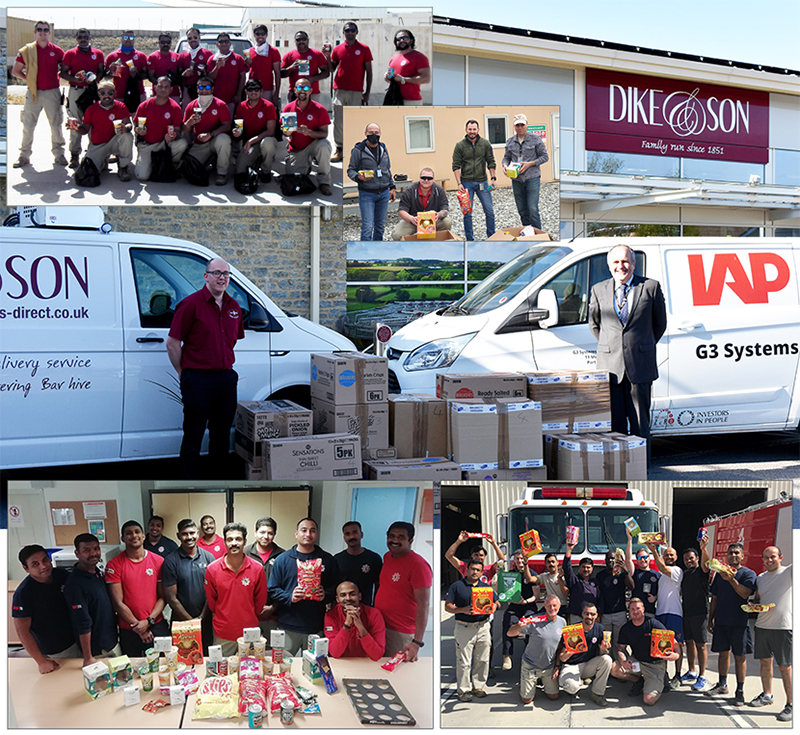
The onset of the CV-19 pandemic and the serious disruption it has created has been even more acute for the G3 teams in Afghanistan. We have some 337 personnel from 25 nations deployed across the four main NATO bases (Herat, Kabul, Kandahar & Mas e-Sharif): due the combination of global travel restrictions and varying degrees of lock down in people’s home nations, they have seen their leave cycles stopped and life on base severely restricted.
Despite this, they have continued to maintain their high standards of professionalism and performance delivery; even finding time to join in the weekly applause for the UK NHS. We continue to do what we can to manage the situation and support our colleagues. This has included sending out welfare packages to the team and we are delighted that Dike and Son, a local independent supermarket chain saw fit to help us by providing items for inclusion in the packages. Our Operations Director Nick Broom collected the packages from the Stalbridge store himself and as we speak the packages are arriving at the bases in Afghanistan. Our heartfelt thanks to Andy Miles, Assistant Store Manager at Stalbridge and the Dike and Son team for stepping up so generously.
Nick commented: “Having met our teams in person in Afghanistan, I cannot commend them enough and I am personally grateful to each and every one of them for the sacrifices they are making. This is a small gesture that cannot compensate for the impact of CV-19 on their lives, but it is to let them know they are not forgotten and to assure them we will do everything we can to support them through these difficult times..”
Army’s AS90 Turret Trainers combined at one site
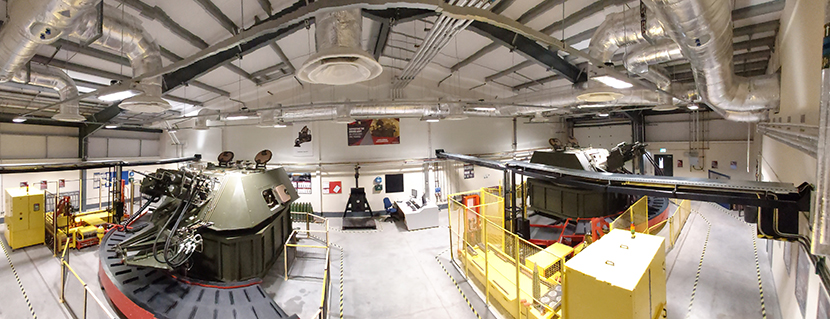
Our long association with MOD DE&S and the Royal Artillery has continued, as our Field Service Engineers have been hard at work, alongside Royal Artillery, MOD DE&S and MOD DIO colleagues, on the project to relocate the Army’s AS90 Turret Trainers.
The trainer was first introduced in 2005 to allow gun crews to practice their routine firing drills, turret operating procedures and crew duties without the expense of live firing. The system offers the immersion and realism of firing, with a reduced safety risk and a highly reduced operating cost.
The systems were originally manufactured by Van Halteren Defence, with whom we have a long and close business relationship. Since their introduction, our Field Service Engineers (FSEs) have been responsible for the operation and maintenance of the system to support the British Army’s Artillery units in conducting training drills.
Based on a real AS90 turret, the trainer uses an electro-mechanical system to fully replicate a complete firing cycle. This includes the weight and size of the artillery rounds and the noise and turret movement on firing. Since the trainer was introduced thousands of Gunners soldiers have used the equipment. The systems include video playback to analyse training performance.
Previously the two systems were in separate locations in the UK and Germany and they have now been relocated to into a combined facility at the RSA Larkhill, which was officially opened by Commander 1st Artillery Brigade.
It’s good to see the systems back in action and now they are co-located at the RSA they will provide an even better training capability, which we are proud to support.
Deployable Engineering Workshop – Training for the Royal Engineers
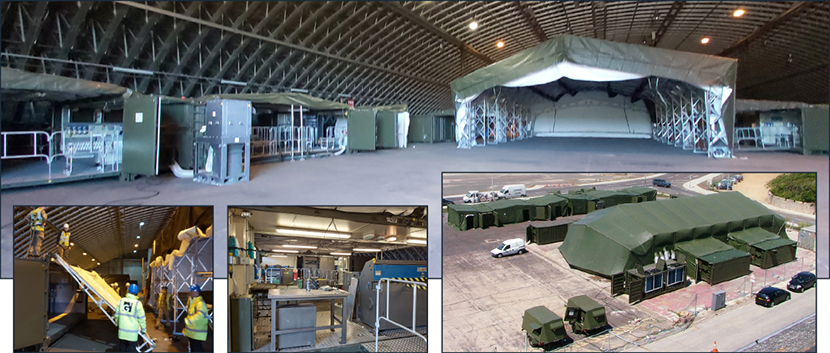
Recently our hard-working Training Team have been deployed alongside our Royal Engineers customers, helping them to reacquaint themselves with the Deployable Engineering Workshop (DEW). The DEW was designed and delivered by G3 Systems to the Royal Engineers over a decade ago and has delivered sterling service in supporting training across the world and on operations in Afghanistan and the Middle East.
G3 Systems has delivered training to numerous Royal Engineer units across the years. This latest session was successfully delivered to 65 Field Squadron, 35 Engineer Regiment at Kinloss, Scotland in March, before full COVID-19 restrictions were imposed.
On this occasion our team – Chris Lacey, Paul Robson-Rowell, Mike Russell and Ashley Wagstaff – deployed to Kinloss to deliver the established training programme in reverse order, taking the DEW down before rebuilding it to leave the users with a constructed system on completion of training. This was the first-time training had been delivered in this way and was extremely effective.
It was important to deliver this training for 65 Squadron – originally to prepare them for a deployment to carry out construction tasks at BATUS in Canada, but now possibly for them to use DEW on operations closer to home. G3 Systems is, as always, proud of our long association with the Royal Engineers and we wish all Sappers well in meeting the challenges of the COVID-19 pandemic. We also recognise and the professionalism and commitment of our G3 team, who ensured that the training was delivered, even as the COVID-19 situation was becoming more fraught.
G3 Systems awarded Investors in People Silver accreditation

We are delighted to announce that Investors in People (IiP) have just awarded us their Silver accreditation. We’ve been committed to IiP for some 6 years as we feel it reflects our commitment to all the members of our G3 Systems family and enables us to benchmark how we look after our people. The Silver award is a great achievement and is something that only 15% of the organisations that IiP assess obtain.
It also reflects the participation of our team in the review process: getting the Silver accreditation has allowed us to confirm what we are doing right, but also where we can improve and keep moving forward. G3 Systems’ HR team is now putting in place an action plan to build on what we learned from the IiP assessment.
To all our G3 colleagues – congratulations on this achievement and your part in it; and thank you for the feedback which will enable us to grow and develop as a team and a business in the future. Well done!
NEWS: G3 Systems article in Tank News International magazine
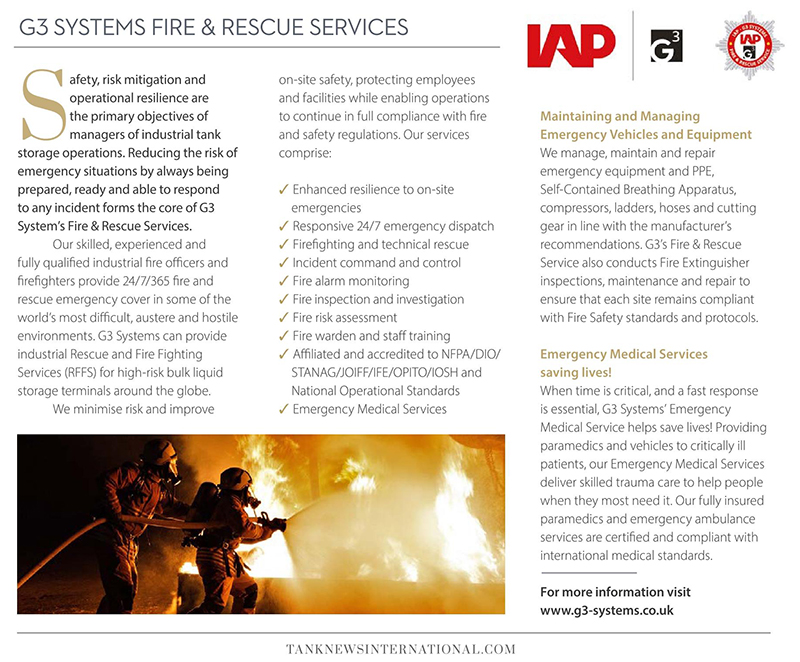
The article highlights G3 Systems Fire Protection Services and capabilities towards the Tank Storage industry.
G3 Systems article in Fire Middle East magazine
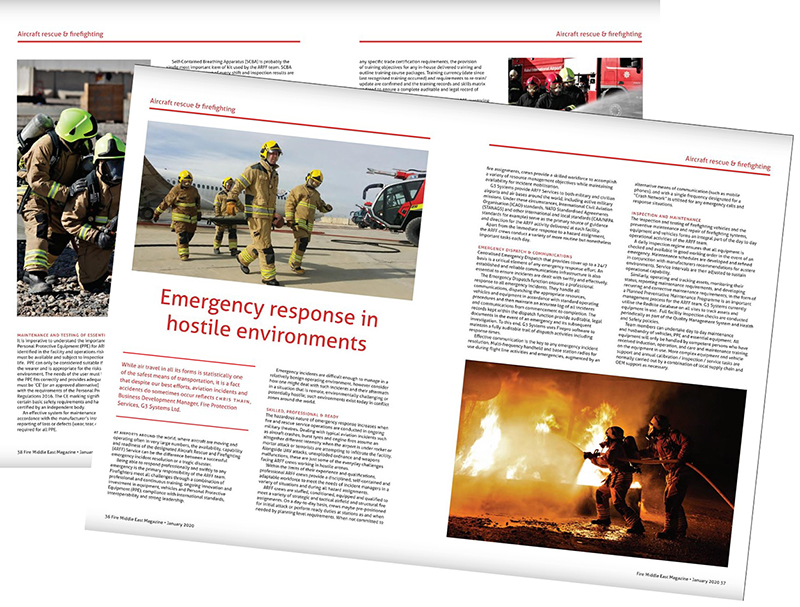
This feature article explores the topic of emergency response in hostile environments – Fire Middle East magazine – January 2020 – Pages 38-41.
To access the full article please click on the logo below.
G3 Systems to provide a Modular Field Hospital to Belgian Ministry of Defence
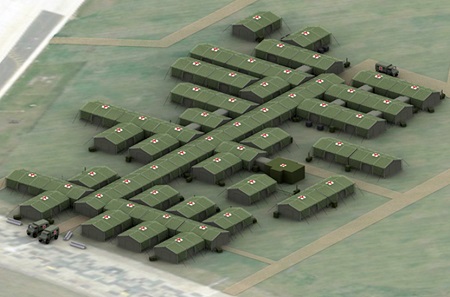
G3 Systems, in partnership with French shelter manufacturer Utilis S.A.S, has recently won a contract to supply the Belgium Ministry of Defence with a modular, deployable Field Hospital. The competition also included bids from Saab and a Dutch-US team of 4 Lutions & Alaska Shelters.
The initial procurement, valued at some US$13.2M, will provide a Role 2 Enhanced Field Hospital, comprising some 54 tents, a medical incinerator and medical equipment ranging from stethoscopes to x-ray machines and a telemedicine system. An additional 19 tents were procured to form the basis for a Role 2 Basic Hospital.
G3 Systems will provide the medical equipment and incinerator whilst Utilis will manufacture the tents and provide the supporting infrastructure. Production will commence in June with delivery to be completed by March 2021. All hospital infrastructure and medical equipment will be consolidated and packaged at Utilis’ facility at Ennery, near Metz in north-west France prior to delivery into Belgium. The value of G3 Systems’ share of the initial procurement is US$7.2M. We also expect additional equipment purchases in the future to fit out the 19 shelters for the Role 2 Basic system.
A full set of technical documentation will be compiled by G3 Systems and training will be provided to the Belgian Armed Forces end user.
Following the completion of the initial equipment procurement phase, a 10 year support service will commence. This will see G3 Systems provide a team of deployable, Field Service Engineers (FSEs) to provide maintenance support for the Belgian MOD on training and operational deployments, coupled with routine maintenance, spares provisioning and options for further equipment procurement. The anticipated value to G3 Systems is US$4M, operational and training deployments may see this increase.
G3 Systems’ Capture Manager, Andy Francis said: “We have worked with Utilis on past projects and were delighted to see the team win this tender. G3 Systems’ ability to source and procure the medical equipment for the hospital and our experience of deploying FSEs into hostile operational areas were the capabilities Utilis needed to build the winning team. We are now looking to market this capability to other militaries seeking deployable field hospital capability solutions.”
G3 Praised for Ground Emergency Response
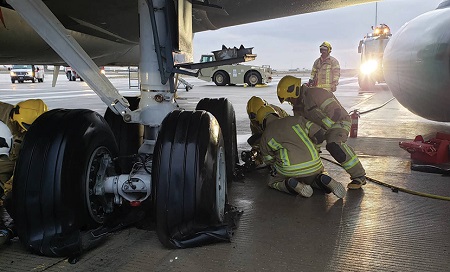
When a Heavy KC 135 blew 8 of its tires at 3:11 on a Saturday morning on a particularly aggressive landing the KAF G3 Emergency Response team were ready to roll. Responding in only 2 minutes the G3 Fire Crews were able to quickly assess the situation, set up incident command and assist in the safe recovery of the plane.
LT Col Kidd of the US Air Force wrote “a few words to express our gratitude for Leon and the entire fire/rescue/crash team for their response and assistance during yesterday morning’s event involving the KC-135 and its 8 blown tires. Our 4 hour 28 minute resolution of the incident was possible because of the professionalism and assistance of your personnel, to include providing hot coffee, tea, and cookies to the additional responders who were working in the cold, wet conditions of yesterday, early morning.”
NEWS: 18th Building handed over to DIO
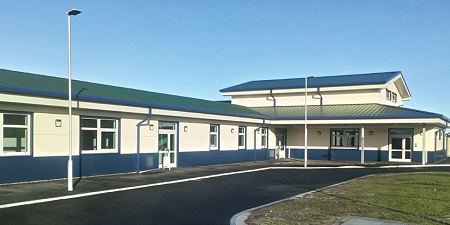
On 27th September 2019 G3 reached an historic milestone with the 18th facility handed over to the DIO in the shape of the Mount Pleasant Primary School on the Falkland Islands.
Started in 2016 the school is a replacement for the existing building at Mount Pleasant that was constructed after the Falklands War ended in 1982.
Now way past its useful service life G3 tendered and won the contract to build the replacement which is a high tech building with ultra-modern facilities throughout including interactive whiteboards in every room and a state-of-the-art building management system controlling the ambient temperature of each of the 5 classrooms all year round.